Automatic Bottle Unscrambler Machines
Acasi Machinery offers a range of bottle unscramblers to accommodate a wide variety of automatic bottle feeding speeds and shapes.
Our bottle descramblers are used to eliminate the labor intensive process of placing empty bottles on the bottling lines. We can provide machines to feed from 1oz bottles to gallons and speeds from 5 bottles per minute to 300 bottles per minute.
Each project is different and once we evaluate your samples, speed requirements and space constraints we can recommend the best automatic bottle unscrambler for your production needs.
Keep in mind that the bottle unscrambler design we offer works with a rotary bowl that can only handle plastic, metal and non-fragile containers.
Once we test in house the bottle descrambler with your bottles we then prepare a setup sheet documenting every adjustment that needs to be done when changing over from one bottle to the other, when our customers follow these procedures the changeover from one bottle to the other takes less than 10 minutes.
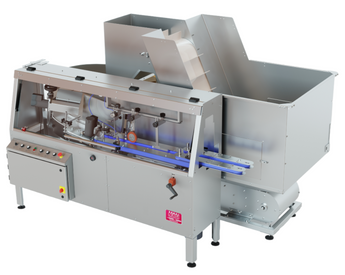
What is a Bottle Unscrambler and Principles of Operation?
A bottle unscrambler is a machine used to feed bottles onto production lines in the bottling industries. Many designs are available, but their purpose is the same, feed bottles automatically at high speeds eliminating the expensive, inefficient manual labor of this process. This article focuses on the principles of operation for plastic and non-fragile containers. Glass, metal, ceramic, and other containers that will get damaged by hitting against each other require different types of machinery like depalletizers for the automatic feeding of those bottles - containers.
How Do Bottle Unscramblers Work?
Bottle unscramblers receive the bottles in random positions since containers are thrown randomly into a large hopper that can hold thousands of bottles. Then those bottles are handled in different ways from the hopper to other parts of the machines, so they are sorted until you get a standing bottle directly in your conveyor going to a bottle filler then to a capping machine, labeler and the rest of the filling line As an example of operation, we will describe our bottle unscrambler model Trusort 48-100.
This bottle feeder brings the containers from the hopper with an inclined conveyor to a rotating bowl; on the rotating bowl, the containers are organized, so they end up only with the neck leading or neck trailing.
After that, we provide a hook that lets the bottles with the neck trailing pass and turn the bottles that are neck leading, so all containers end up laying down with the neck following.
After that, there is a step between the speed difference between the two sets of belts and the mechanical design that stands up the containers. This explanation will be easier to understand if you can review a few of these videos.
This is a basic explanation; there are thousands of bottle designs, and each container needs to be analyzed for a bottle unscrambling machine to work correctly, take into consideration, among other things:
1. Required Speed
Since the bottle unscrambler is at the beginning of the bottling line, it needs to be the fastest machine to make sure that it can catch up with any of the other filling equipment in the line if there is a stoppage.
2. Container size
Container size in liquid filling machinery is critical for machine size recommendation; for example, a 32 in bowl machine can do 200 + bottles per minute of a 2oz bottle, but it will only do 10-15 bottles per minute on gallons. Also, a 25 cubic foot hopper can accommodate thousands of 2oz bottles so the machine can run for a long time without any operator, but it can only accommodate a few dozen gallons, so the unscrambler could only run for a few minutes before the hopper has to get filled again.
3. Design features
Each container design feature on a container can present a challenge on any part of the unscrambling process; it can be too soft, ridges that damage the container, dimensionally hard to orient (Bottle diameter and height are similar), guides on the bottle that catch the hook, among other things.
4. Installation location
A lot of production lines start without a bottle unscrambler, and when analyzing the possibility to add one, there is no good space to place it on a liquid filling line since these machines tend to be on the largest of the production lines. Normally it’s placed before the liquid filler or powder filling machine. Some customers also install the unscrambler machine right before the labeling machine when it’s convenient to label the containers before the liquid filler.
5. Material
Container material, the possibility of marking and scratching, fragility, quality issues are a few of the challenges we encounter getting our machines to work properly, pet bottles may require special handling to avoid scratches while getting sorted on the PET bottle unscrambler.
6. Cleaning containers on unscramblers
We offer air rinsing option on our unscramblers but it’s important to note that the cleaning done on this systems with ionized air or ionized air rinsing is minimal, for containers that require cleaning a dedicated bottle rinser is recommended.
Secondary Orienting
To automatically feed containers into a production line, some containers require secondary orienting so the containers are in the right position before going into the liquid filling machines or packaging equipment. Additional orienting is necessary when the bottle coming out of the bottle unscrambler gets delivered into the conveyor in many positions; an example of this would be a motor oil quart with the off-center neck. On a typical bottle unscrambler, the containers will feed these nonsymmetrical containers either neck leading or neck trailing, so to automate the packaging line, you need to add secondary orientation.
Each container has its particular challenges, and based on this; there are many types of secondary orientors, among the most common are:
- Container orienting grabbing with belts by the neck: This is an inline system that holds the container by the neck and uses either the shape of the container with mechanical guides to orient or uses servo or stepper motors on each belt, then with sensors or cameras determines the container on the non-desired position and sends a signal so the differential in speed orients the container by the neck. The process is shown in this video.
- Container orienting with side guides servo-driven: This machine has sensors and cameras that detect the container in the wrong position, and it mechanically turns at very high speed (servo driven) the container 180 degrees :
- Container orienting on rotary machines: These machines handle the container with infeed screws and starwheels onto pedestals that rotate the containers based on their position given by sensors or cameras. When handling unstable containers or high speed is required is the only way to go. The problem is the cost of the machine as well as the change parts pricing.
There are many designs in the packaging machinery industry that can accomplish the desired bottle feeding into packaging machines. We chose this design because it provides flexibility to handle a wide range of containers with very few change parts. Designing an automatic bottle unscrambler as efficiently as this one makes it less expensive, making it more accessible to our customers. Above 500 bottles per minute, a continuous, rotary unscramblers can handle those speeds; the main drawback is cost, space requirements, and change parts costs.
Acasi Machinery
Our company specializes in innovative capping solutions designed to streamline and enhance your production efficiency. With a commitment to quality, we offer a wide range of capping machines tailored to meet the unique needs of industries worldwide. Backed by years of expertise, we strive to deliver reliable equipment that ensures precision and consistency in every operation.